Australia’s fast-growing population especially with the resumption of immigration following earlier COVID border closures, has presented challenges for governments in meeting infrastructure requirements to successfully accommodate additional residents.
Expanding civic services such as educational facilities is important to properly welcome and integrate newcomers while forming a key pillar of the broader community – but the problem is that schools can’t be built overnight. Traditional large scale building programs can take years to complete by the time the various planning, design, engineering and ultimately construction works take place.
Anybody who went to school in the 1970s through to 1990s will likely remember the ugly, prefabricated school portables; ‘temporary’ box-like classrooms that were often used permanently for years – cold in winter and hot in summer, but they were efficient to install.
So the concept of prefabricated classrooms certainly isn’t a new one, but it’s an idea that’s definitely evolved and improved over time.
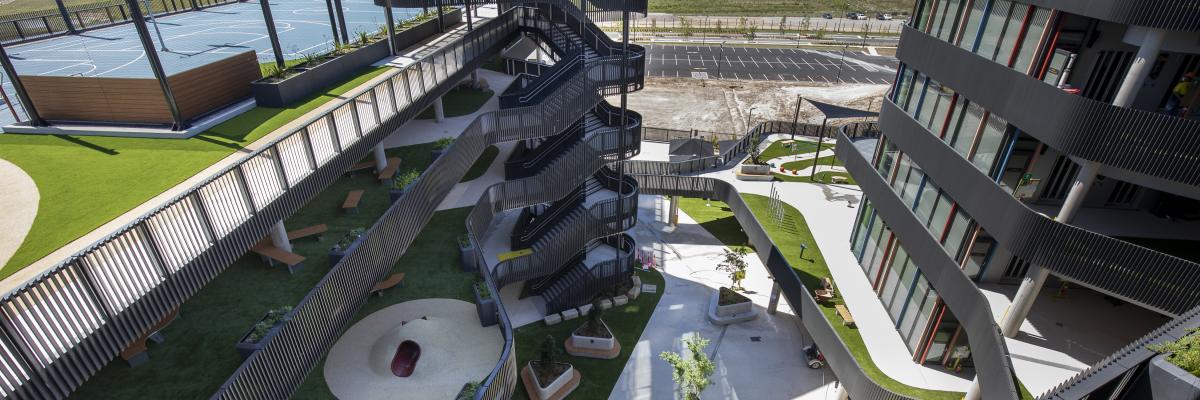
A recently completed multi-storey school building at Santa Sophia Catholic College in Sydney’s Box Hill, shows what is possible using the latest prefabrication technology. The new co-educational Kindergarten to year 12 school can cater for up to 1,850 students and 130 full-time staff members, and amazingly it was constructed in just 16 months.
The fast build time wasn’t achieved at the expense of quality or mundane design either. The project consisted of five building zones, each rising to between four and six storeys and connected by podiums full of interactive play elements suited to the different student age groups. Facilities are also multidimensional and include collaborative learning areas, creative and performance hubs, open spaces and more.
Built by leading construction company Buildcorp in conjunction with key partners including BVN Architects, TSA Project Managers and Northrop Structural Engineers, all stakeholders on the Santa Sophia Catholic College project worked closely to shape the building design from the outset using an off-site prefabrication approach and building information modelling (BIM).
A robust prefabrication strategy was devised that included using pre-cast concrete core and walls and sourcing pre-built structural steel framework from 16 sites to minimise supply chain risks. Curtain wall and modularised framing was also developed, while off-site manufacture of 70 per cent of the joinery and interior paneling took place.
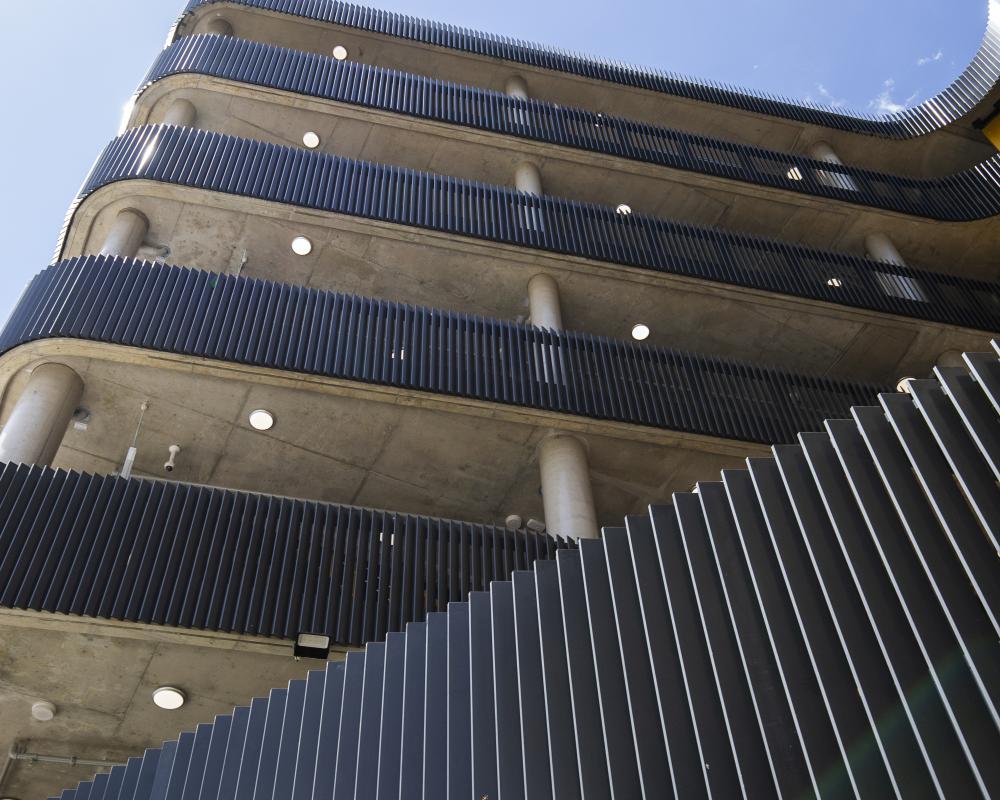
Fielders’ Business Development Management (BDM) team was also asked by the Buildcorp to be involved at the early contractor stage, assisting the architectural team and consulting engineers to design and deliver a fully coordinated and unpropped structural steel building solution. The solution saw Fielders KingFlor® range of composite steel formwork products, including SlimDek 210® and KF70®, used on four of the five interconnecting buildings.
As part of the overall service offering, the Fielders BDM team provided structural value engineering, construction staging, detailing and broader advice to improve the construction program to help reduce project costs for the builder while helping tight building schedules to be met. Fielders National Engineering Manager, Marko Stankovic explains further.
“Our in-house structural engineering team utilised its expertise in composite design to develop the most cost effective and program efficient composite steel building structure for the client.” Marko said.
“Leveraging our in-house BIM expertise, we facilitated holistic project coordination between structural steel framing, Fielders KingFlor® composite metal decking, hydraulic services and structural bracing elements, in a cloud based live 3D Digital model.
“All stakeholders used this model to collaborate with other disciplines and installers to fully integrate and coordinate SlimDek 210® and KF70® into the project. This process allowed real-time multi-disciplinary clash detection and resolution to occur at the design detailing stage, significantly reducing on-site service installation issues. The model was also used to produce full metal decking shop drawings and cutting lists used for manufacturing of sheets and set out on-site. This led to improved safety outcomes, reduced waste and works on-site.
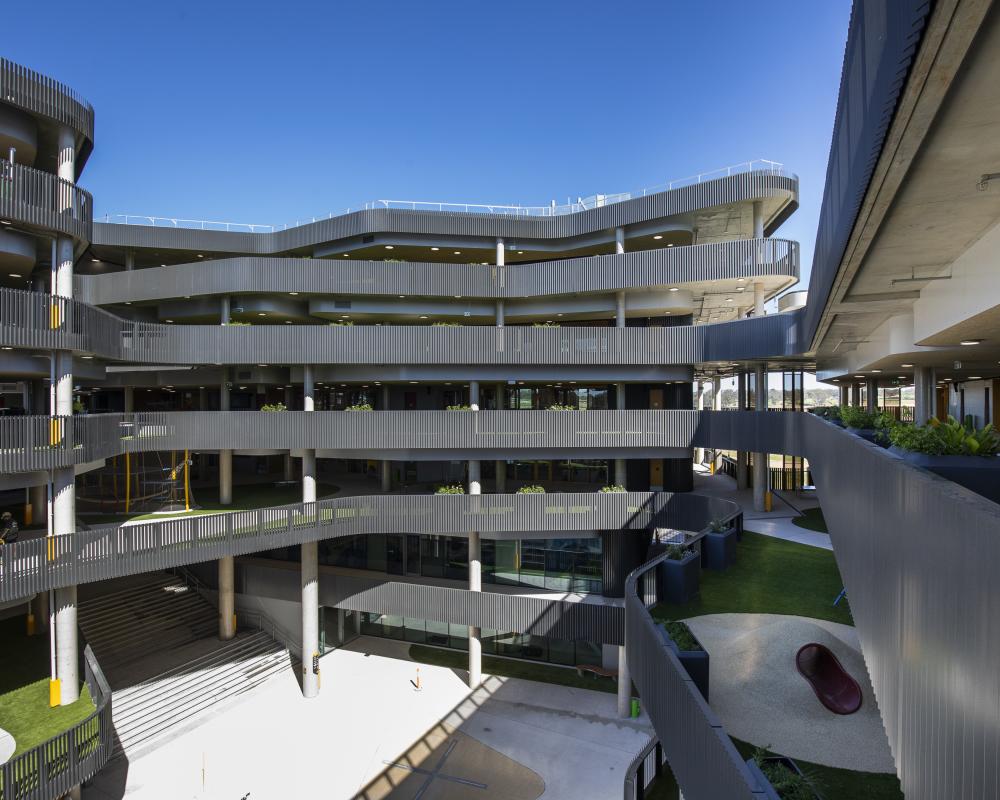
“The fully unpropped structural steel and SlimDek 210® design solution led to significant reductions in time spent on building a floor, and consequently allowed immediate fit-out of floors below, compressing the construction program and allowing the builder to meet their strict program deadline.”
According to Buildcorp Project Manager, Paddy Holland, having Fielders involved in the project at an early stage delivered added efficiency and helped to address any queries that Buildcorp had.
“This was the first time I’d used Fielders permanent formwork, and the team was able to talk me through the process and make recommendations to ensure all our objectives would be achieved,” Paddy explained.
“As a builder we were pleased by the efficiency the Fielders systems provided – there was no back propping needed, meaning construction was much faster.
“The Fielders team was also readily available throughout the project to lend support if needed. I wouldn’t hesitate to use the Fielders permanent formwork again on future builds,” he said.
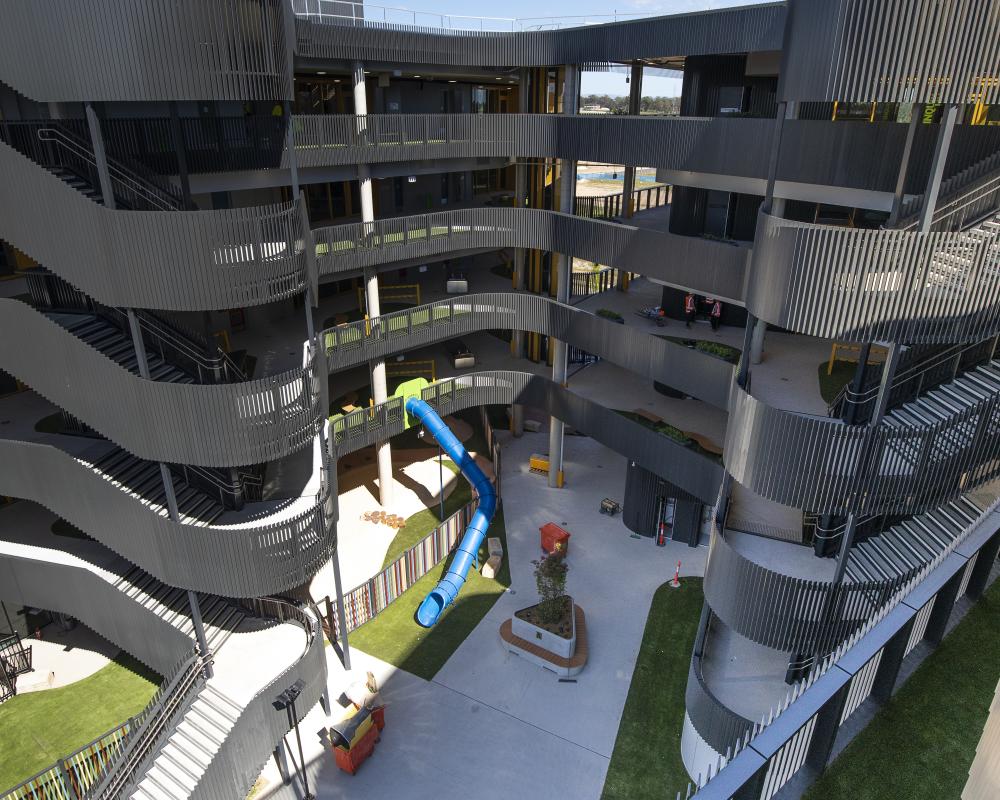
About Fielders permanent formwork
The Fielders KingFlor® range of permanent formwork, such as SlimDek 210® and KF70® profiles used at Santa Sophia Catholic College provide engineers, builders and installers with several benefits.
Conventional plywood formwork involves considerable time, labour and resources to set-up and back-prop before a concrete pour can take place. Furthermore, once the concrete has cured, additional labour is required to remove back-propping and strip the plywood formwork. Permanent metal deck formwork like Fielders KingFlor® stays in place after the concrete has set and has superior unpropped spans, reducing the back propping requirements and labour on site.
The wide range of KingFlor® profiles host a range of benefits for end users in various building applications. The trapezoidal geometry of KF40®, KF70® and SlimDek 210® enables significant savings in reinforcement as well as concrete volume savings by displacing concrete where it’s not needed, reducing cost while satisfying even the most stringent floor performance requirements. The cost efficiency and program advantages achieved by KingFlor® composite decking is unrivaled compared with traditional construction practices.